The protection against corrosion of iron can be made by the use of stainless iron in place of metallic iron, protective paints such as zircon or tin, and by means of sacrificial metals, which is the technique used in electroplating in that there is cathodic protection.
As stated in the text ” Corrosion of Metals “, the corrosion of many metals, such as iron, causes great economic and social damages.
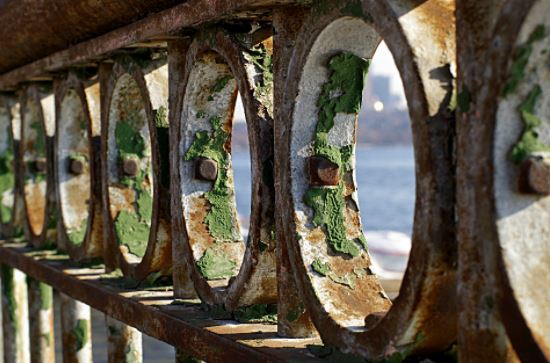
Silver, aluminum, and copper are not very corrosive because when they oxidize they naturally form a kind of protective film that prevents the rest of the material from being subjected to corrosion. In the image below it is possible to see what is the constitution of the protective film in each case
Iron, however, rust, forming Fe2O3. 3H2O, which is not a protective film. On the contrary, the rust on the metal surface is releasing and continuously exposing the metallic iron to the ambient condition. In this way, the corrosion continues until the total deterioration of the part. Thus, scientists, especially chemists, have developed methods of protection for iron and steel, since they do not have a natural protection process.
Some of these methods are presented below:
Coating: Iron can be prevented from being in contact with oxygen from the air for many years by applying a layer of protective paint, such as zircon (Pb 3 O 4) or other more efficient polymer-based paints.
One can also coat tin, as is the case of the Flanders sheet used in canning. It can be covered by an extra layer of polymers in the inner part, because the citric acid present in the stored foods can react with tin and iron, contaminating the food.
Sacrificing metals: this technique is also called electroplating in honor of the scientist Luigi Galvani (1737-1798).
In it a metal coating is applied to a part, placing it as a cathode (negative pole) in an electrolysis circuit.
The iron is protected by using a metal having the potential for oxidation greater than that of the metal, such as magnesium and zinc. When the metal used is zinc, it is called galvanizing.
The metal used is called “sacrificial” exactly because it is it that will be oxidized in place of iron. This sacrificial metal loses electrons to the iron keep it protected even if the surface is scratched and the iron is exposed to the air.
This is not the case with tin, which only prevents the iron from coming in contact with the air. Once this layer of tin protection is broken, the iron will rust quickly.
In electroplating, the improvement of the part is achieved, in addition to the protection, as it is similar in appearance to the more coveted metals such as gold and silver. Examples of electroplating include chroming, silvering and gilding.
The sacrificial metal must be changed from time to time because of wear.
A similar process is to attach plates of magnesium or zinc to those of iron. This is done to protect the hulls of ships and the stakes of the oil rigs.
Stainless steel: (iron and carbon alloy) becomes stainless by mixing it with other metals such as chromium, nickel, vanadium, and tungsten.